Evolution of Industrial Safety Culture in India:
A Journey Towards Awareness and Empowerment
It all unfolded on an ordinary day when absorbed in his work, Manoranjan received a call that would forever alter the course of his life. His wife, Lekha, suffered a heart attack while tending to household chores, leaving their family in a state of panic. With 5 adult members present in the family, chaos ensued as they scrambled to fight for the life of Lekha. The wrenching truth is that Manoranjan had learned about CPR during mandatory first aid training at his workplace, yet he couldn't pass this knowledge on to his family. The profound impact of the gap between knowing and not knowing now shadows Manoranjan's existence.
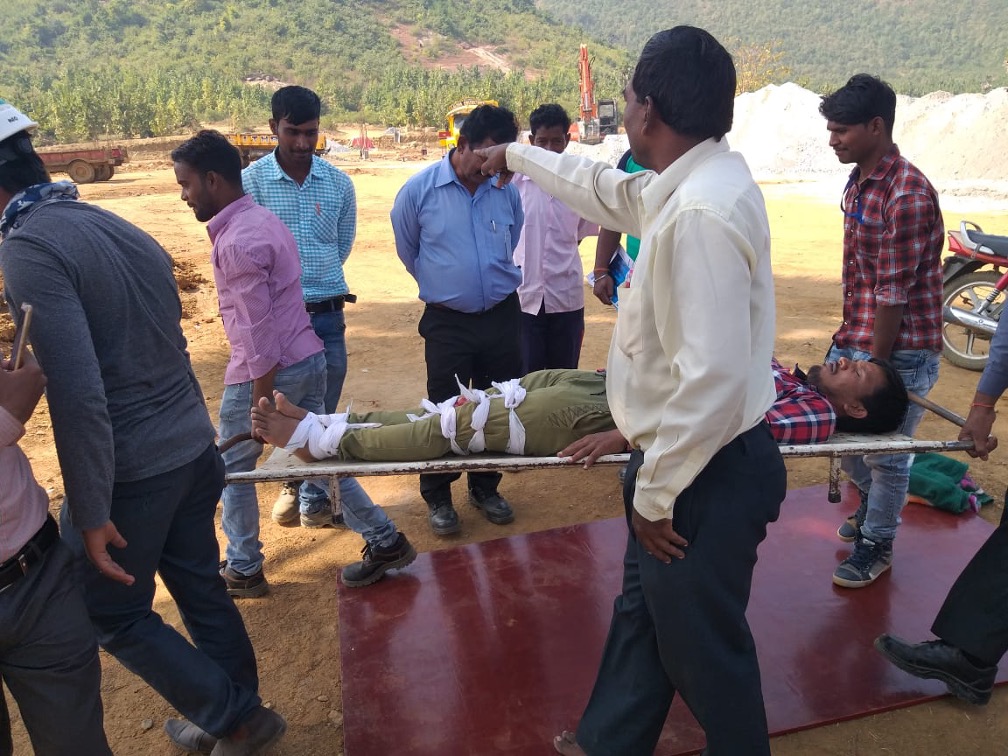
The history of industrial safety in India is a compelling narrative of transformation, from heart-wrenching tragedies to a gradual shift towards a safety-conscious society. The Bombay Explosion of 1944 stands as one of the earliest industrial disasters in India, claiming thousands of lives and leaving widespread devastation in its wake. Similarly, the Chasnala mining disaster of 1975, depicted in the movie "Kala Patthar," offered a stark portrayal of the dire outcomes of lax safety practices in the mining industry. These heart-wrenching events served as sobering wake-up calls, urging us to prioritize safety in our industrial endeavors. The Bhopal Disaster in 1984 was a pivotal moment in India's industrial history. These events reinforced the urgent need for comprehensive safety regulations and rigorous enforcement. As time has passed, a significant shift towards a more human-sensitive approach to safety has emerged, emphasizing awareness and prevention over mere reaction.
This article delves into the broader implications of industrial safety and health awareness, highlighting its influence on socio-economically disadvantaged individuals beyond the confines of industrial premises. It provides insight into the present landscape by featuring testimonials from individuals occupying the lowest rungs of the workforce hierarchy. Additionally, the article offers recommendations to guide the ongoing transformations in the realm of industrial safety in India.
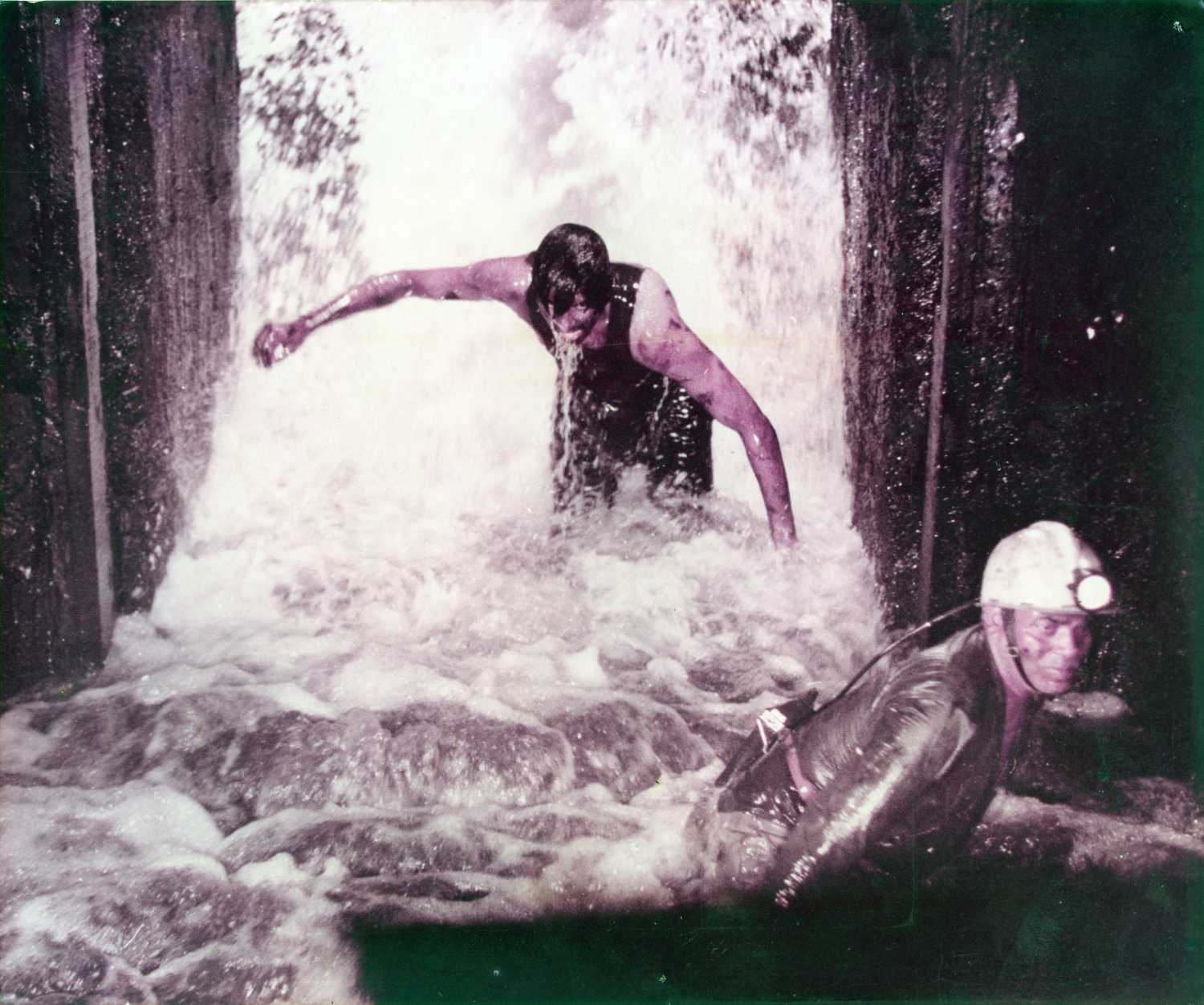
In the wake of the industrial disasters that scarred India's history, a series of pivotal safety standards and regulations were introduced to address the critical need for occupational health and safety in the country. These regulations, gradually but consistently, have been instrumental in shaping and improving the safety landscape in India.
The Factories Act, 1948, was one of the earliest legislations aimed at safeguarding the well-being of workers in industrial establishments. It laid down regulations pertaining to the health, safety, and welfare of employees, addressing issues such as working conditions, ventilation, and hazardous processes.
Subsequent legislations, such as the Dock Workers (Safety, Health & Welfare) Act, 1986, the Building & Other Construction Workers’ Act, 1996, and the Child & Adolescent Labour (Prohibition & Regulation) Act, 1986, have further expanded the scope of safety regulations. These laws encompass a wide range of industries and occupational scenarios, reinforcing the commitment to safeguarding the lives and well-being of workers.
The government has realized that safety isn't limited to worker health but also extends to environmental protection. Acts like the Air (Prevention & Control Of Pollution) Act, 1981, and the Water (Prevention & Control Of Pollution) Act, 1974, were established to mitigate the environmental impact of industries, contributing to a healthier, safer society. The government laws were well received by large-scale industries in the country, this resulted in the formulation of industry-wise safety policies, on-site emergency plans, and safety committees to implement the regulations at the lowest possible points of the work hierarchy. The implementation of these safety laws and policies in India reflects a commitment to prioritize the welfare of workers and the environment. While the journey towards a fully secure industrial landscape is ongoing, these regulations serve as milestones, shaping India's path to occupational health and safety. They underscore the importance of prevention, consciousness, and the sanctity of human life, ushering in an era where safety is not just a legal requirement but a way of life.
Manas Jena, a 32 years villager in a small village of the Dhenkanal district of Odisha, who works as unskilled labour in a green field project site. Until about nine months ago, He was just an ordinary farmer, working the fields of the village. He had never been to school. He lives with his family consisting of a 28-year-old wife, and a 4-year-old child. Manas expresses the shift that he experiences after being a part of the industrial workforce,
“Swear to God, I had never thought about these things before. But now, as an industrial worker, I understand the value of safety, and I'm grateful for the opportunity to learn. It's not just about earning a living; it's about ensuring that life, in all its precious forms, is protected.”
“What surprised me the most was how this newfound consciousness about safety and the environment began to seep into my everyday life outside of work. For the very first time, I started to pay attention to electrical hazards at home, especially when a 4-year-old kid is roaming around my small place. I made sure wires were not frayed, and plugs were in good condition. I understood the dangers, and I took steps to keep my family safe.Another change I made was wearing a helmet when I rode my bike. It wasn't something I used to do, but after becoming habituated to hard hats at the workplace, I couldn't ignore it anymore. I realized that safety wasn't confined to the workplace; it was a responsibility I had towards myself and my loved ones, no matter where I was.”
"I wear a helmet not because they tell me to, but because I understand its importance. I've taken this message home, and now, I ensure my family follows safety precautions too. It's about returning home safely every day, and that's what matters most."Another co-worker of Manas added.
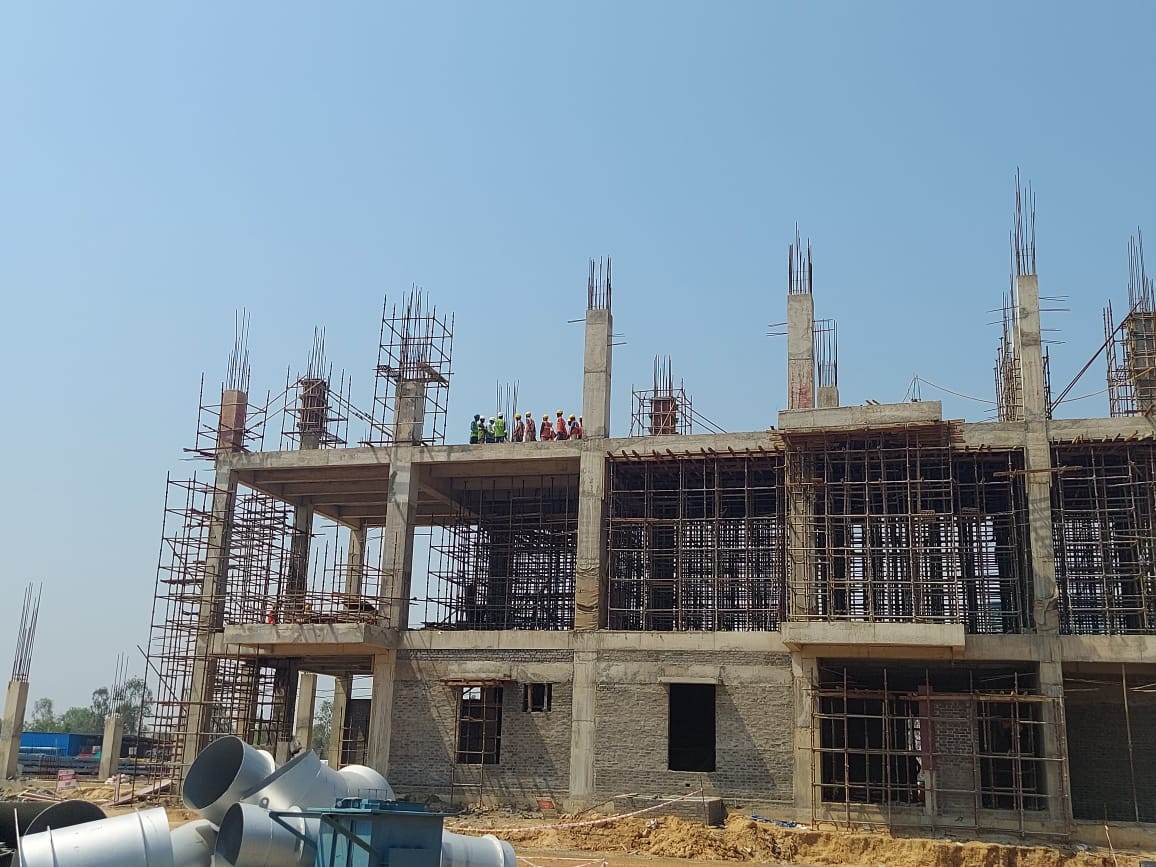
Similar to Manas, there are numerous accounts of laborers who have not had the opportunity to acquire a formal education. Their knowledge of first aid methods, hygiene practices, and environmental conservation has been exclusively gleaned from the diverse Health, Safety, and Environment (HSE) initiatives instituted within the organization where they earn their livelihoods. Insights into crucial matters such as responding to snake bites, administering CPR, or understanding the detrimental effects of minuscule dust exposure on their later years, all accrue as an incidental benefit tied to their salaries. For these laborers residing in economically disadvantaged regions of Odisha, ‘Information’ represents the sole incentive they receive.
Manoranjan Das is a 48 year worker, who works as civil construction labor at a steel plant located near Angul (Odisha).
‘It was the first week of August in 2021, I was at work. Little did I know that my world was about to shatter. At home, my wife, Lekha, was going about her daily chores when, out of nowhere, she suffered a heart attack. Our modest home was filled with our 21-year-old daughter, 19-year-old son, my 64-year-old mother, my 45-year-old brother, and my 40-year-old sister-in-law. A total of 5 members were present in the house when suddenly Lekha fell on the ground. Chaos ensued as panic gripped each one of them. They frantically ran in all directions, desperately seeking help from our neighbors and the only doctor in our village. It felt like an eternity, but the doctor finally arrived 20 agonizing minutes later. Lekha was rushed to the nearby government hospital, but by then, precious 45 minutes had passed since the incident.’
‘The cruel twist of fate was that I had learned about something called CPR during one of the mandatory first-aid training sessions provided by the steel plant. If only one of them had known how to administer CPR, Lekha might still be with us today. The gaping chasm between what I knew and what my family didn't know has left a profound and lasting impact on my life. The guilt and sorrow I feel are immeasurable, a constant reminder of the tragic consequences of that fateful day.’
HSE programs implemented in workplaces often serve as a valuable source of knowledge for underprivileged segments of society. Taking a cue from Manoranjan's experience, safety isn't confined solely to the workplace; it extends to every facet of our lives, regardless of our location or activity. Policymakers should recognize that this informal education regarding health and safety holds significant importance in someone's life. Safety committee meetings, safety discussions, or similar events may not guarantee a permanent impact on an individual's life. However, what they can genuinely accomplish is to spark curiosity, guide individuals toward further knowledge, and uplift the living standards of economically disadvantaged communities in terms of health and hygiene.
The commendable HSE culture observed in developed nations can be attributed to having a highly trained, qualified, and standardized workforce. Given that we currently lack a skilled and educated workforce in India, it becomes imperative for us to take a distinct approach. Industries must take the lead in establishing benchmarks and providing international-standard training to their employees. The skills, knowledge, and, most importantly, the motivation gained in the workplace are likely to permeate into the communities from which these workers come, ultimately returning as a transformative force.
Debasish Dey is a qualified oil and gas pipeline welder who has worked in countries like Saudi Arabia and Kuwait. He explains his experience, ‘Safety culture abroad, particularly in Saudi Arabia, was markedly different from what I've observed in India. Every aspect of the job was meticulously planned and executed without any second thought. Comparing these experiences to India, I noticed several differences. In India, while safety measures exist, their enforcement can sometimes be lax, particularly on smaller construction sites. PPE compliance isn't consistently monitored, there's often a rush to complete projects, which can sometimes compromise safety standards.’
When asked about the reason behind the drastic difference could be, he replied, ‘Factors such as resource constraints, varying levels of awareness, and economic pressures can influence safety practices in India. In my experience, the intensive safety culture abroad was not just necessary but added immense value to the job. It ensured that workers returned home safely each day, physically and mentally unharmed. It reduced accidents, injuries, and fatalities significantly.’ He added.
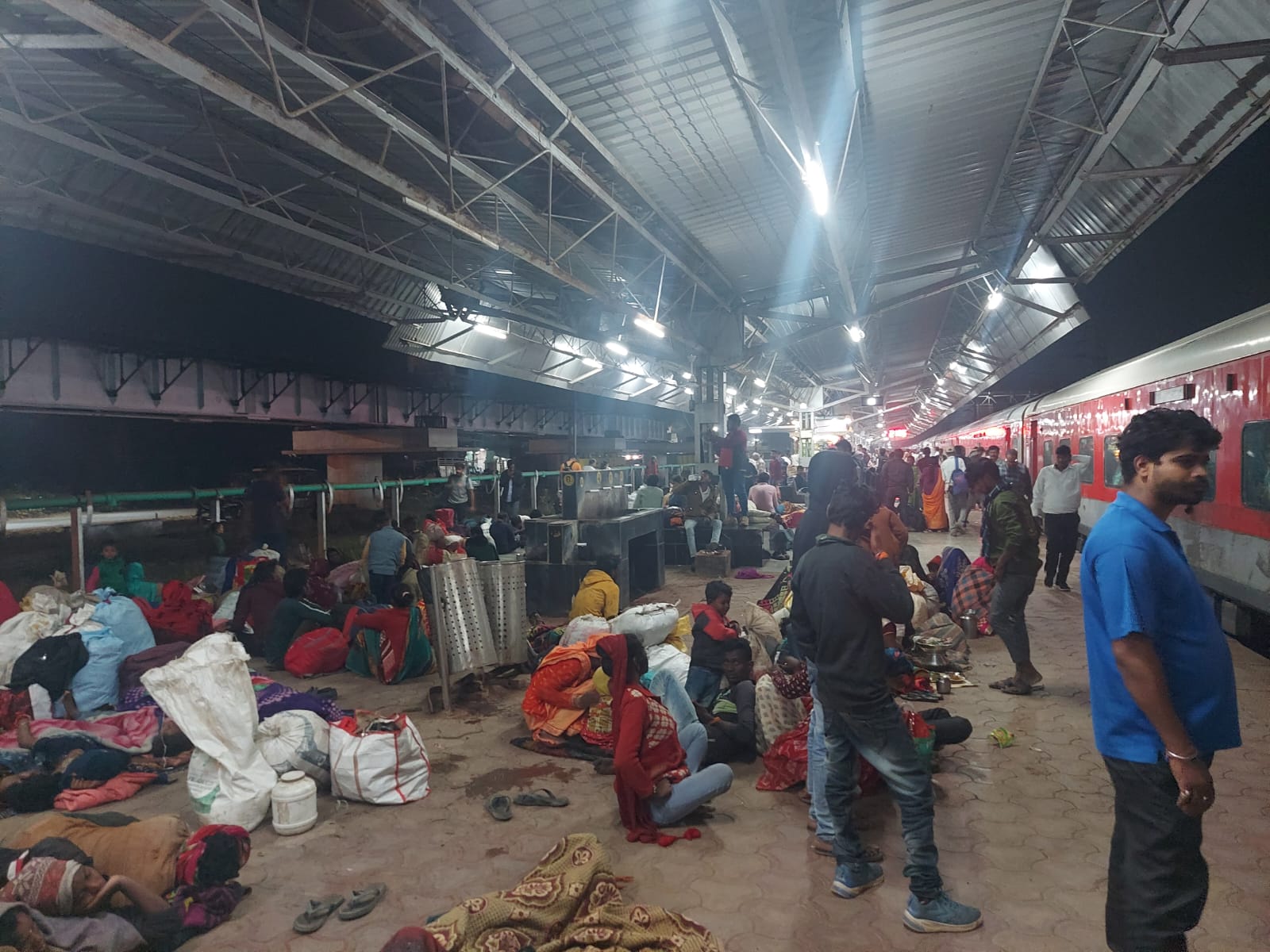
India is experiencing a gradual but definitive shift towards a culture of industrial safety. This paradigm shift places significant emphasis on a human-centric approach, with industries recognizing the paramount importance of prevention and heightened awareness. While it's evident that there remains a substantial journey ahead to match the safety standards of developed nations, there's no denying that encouraging developments are already in motion.
Deborat Monal is a Veteran when it comes to the construction of hydrocarbon Oil Storage Facilities. He started as a helper in 2002, and now (2023) he is supervising the whole team working on the construction of an internal floating roof tank in Haldia, West Bengal. "The contrast between my early days is remarkable, reflecting a profound shift in safety awareness, industrial health, and a significant reduction in casualties. The main issue was that we were not aware that hazardous gas from welding fumes would become the reason behind my heavy medical bills, and there was no one to tell us.”
(Silicosis and noise-induced hearing loss are the most common occupational health diseases among industrial workers in India)
“In 2004, during a routine maintenance task at one of the storage tanks, a colleague encountered a gas leak. There were no gas detectors, and the alarms were virtually non-existent. It was only when he started feeling dizzy and nauseous that he realized something was wrong. We rushed him to the hospital, but it was a close call. Thankfully, he survived, but it was a wake-up call for all of us.” He adds.
“Today, the emphasis on safety is not just about compliance with regulations; it's about a shared commitment to ensuring that every worker in my team returns home safely.”
Taking the lead from the stories, one may try to find answers to the following questions through quantitative research,
As detailed in the initial portion of this article, workers were once perilously exposed to hazards in their workplaces, and this led to major industrial disasters. However, there has been a substantial departure from this perilous past. A telling example of this evolution is the newfound commitment to the well-being of workers beyond the factory gates. Nowadays, industries are not only focused on workplace safety but are also extending their efforts to provide first aid training, medical check-up camps, and hygiene kits to workers, ensuring their safety and health in their homes and communities. This transformative shift represents a significant leap forward in safeguarding the lives and well-being of the workforce.
What the industry and government need is to keep their best engineers and managers at the top of their health and safety departments. Fostering safety or promoting occupational health does not directly add to the revenue of the organization, but the intangible benefits are significant if properly evaluated. Engineers and managers in influential positions now bear the profound responsibility of elevating socially and economically disadvantaged sections of society to the same level of safety awareness. Industrial safety initiatives have transcended the confines of the workplace, reaching out to communities, and fostering health, environmental, and safety education among those involved.
Safety has transcended the boundaries of the workplace, becoming a fundamental aspect of our lives. These changes are gradually enhancing the lives of disadvantaged groups, instilling a profound appreciation for the sanctity of human life, and fostering a sense of social responsibility. As India continues along this path, it is vital to recognize the significance of a human-sensitive approach to safety and its transformative impact on society as a whole.